CPIM 8.0
The APICS Certified in Planning and Inventory Management (CPIM) program is globally recognized as the gold standard in production and inventory control. Holding an APICS certification signifies a dedication to excellence, boosting your value to employers, enhancing earning potential, and paving the way for career growth. The CPIM program is structured into modules over two parts, ensuring a comprehensive education and a solid knowledge foundation.
With over 100,000 professionals certified in CPIM 8.0 and nearly 3,000 achieving the prestigious APICS Certified Fellow in Planning and Inventory Management (CFPIM) designation, this program is a testament to expertise and leadership. Earning the CFPIM designation further sets you apart, recognizing your commitment to sharing your expertise through presentations, publications, teaching, and active involvement in professional development.
Why CPIM 8.0
- Globally recognized as the top certification in Planning and Inventory Management
- Boosts earning potential and accelerates career progression
- Enhances internal operations, elevating customer satisfaction and driving company profits
- Expands your expertise in planning and inventory management
- Opens doors to global career opportunities with internationally acknowledged credentials
- Strengthens your professional reputation and marketability
- Equips you to bring innovative solutions to suppliers, manufacturing, and distribution
- Incorporates the latest best practices to elevate job performance, drive organizational improvement, and optimize planning and operations
- Boosts your credibility and influence within your organization
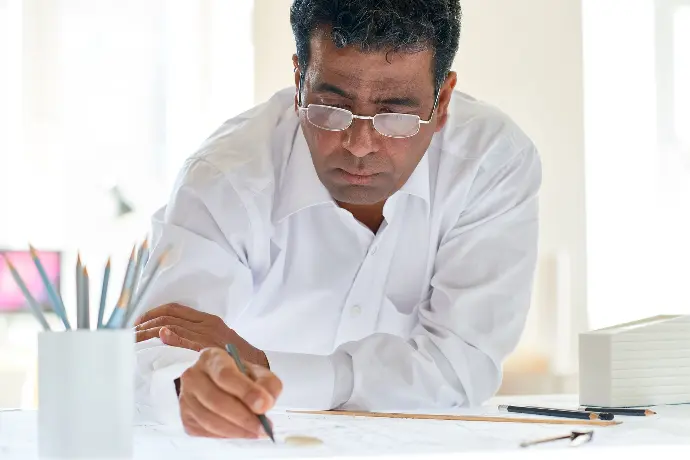
CPIM learning system modules
- Supply Chains, the Environment, and Strategy
- Strategic Scope and Objectives
- Developing and Managing Organizational Strategy
- Functional and Operational Strategies
- Environments, Types, and Layouts
- Performance Monitoring and KPIs
- Risk Management
- Capital Equipment and Facilities
- Sustainability Strategies
- S&OP Purpose and Process
- Aggregate Demand and Supply Plans
- Reconciling S&OP Plans
- Demand Management
- Sources of Demand/Forecasting
- Forecast Performance
- Creating and Validating the Master Schedule
- Using and Maintaining the Master Schedule
- Material Requirements Planning
- CRP and Scheduling
- Suppliers and Purchasing
- Changes and Product Life Cycle Management
- Planning Detailed Schedules
- Scheduling and PAC Methods
- Creating Production and Service Schedules
- Managing Detailed Schedules and Scheduling Materials
- Inventory Planning
- Inventory and Product Costs, Value, and Metrics
- Itemized Inventory Management
- Inventory Control
- Planning Distribution
- Replenishment and Order Management
- Waste Hierarchy and Reverse Logistics
- Quality
- Technology
- Continuous Improvement